Shopping Cart [more]
Index of Products
- Laminator Replacement Parts
- School Laminators
- Laminators by Manufacturer->
- Pouch Laminators / Pouches
- Laminating Films
- Nap I and Nap II Films, GBC Laminating Films
- DigiSeal Laminating Film
- Opti Clear Laminating Film
- Tamerica Laminating Films
- Durafilm Laminating Film
- Cutters and Trimmers
- Dry Mount Tissues, Foam Board/Presses
- Expression Mechanical Presses
- Foam Board
- Olfa Products
- Pressure Sensitive Products
- Roller Cleaning
Information
Laminating Problems And Solutions
Wrinkling of the film
1.1) The film will wrinkle if there is not enough supply roll tension. Any laminator needs a certain amount of resistance to the unwinding of the supply rolls so that the film lays flat as it goes into the nip of the laminating rollers. Turn the rolls of film (supply rolls) in the unwind direction. Is there some resistance? On a 25" machine with 3-mil film, two turns of tension on each knob should be about right. Thinner film needs less tension, thicker film needs more. Loosen both supply roll knobs until tension on the spring is released. From the point where each knob just begins to press on the spring, add the correct tension by half turns. (Four half turns equals two turns, for example.) DO NOT use too much supply roll tension. A larger laminator with 5-mil or heavier film may require 4-5 turns of tension on each knob. It's unusual to need more than 5-6 turns of tension even on bigger laminators. Remember, you are not concerned about wrinkling of the film on the shoe. You are only concerned about wrinkling you can see in the finished work.
1.2) Make sure the film path is correct for both top and bottom webs. Make sure the film is threaded around both the top and the bottom idlers. Take a look at the film threading diagram in your operators manual. (P.S. An Educator does not have a top idler.)
1.3) Make sure the machine is up to temperature. The film should clarify just as soon as it hits the heated areas (the two black parts we call the shoes). If the laminating and pull rollers on your machine can be opened and closed,
make sure both sets of rollers are closed.
1.4) If the top looks fine, but the bottom shows lots of bubbles and wrinkles, the bottom idler is probably not threaded. Look at the threading diagram for your machine. (P.S. An Educator does not have a top idler.)
Wrinkling of the paper
2.1) Make sure you feed the item so that the leading edge is parallel to the laminating rollers. If the item is not laying flat and smooth when it goes into the laminator, it cannot be expected to come out flat and smooth. If an item has been rolled, folded or wrinkled beforehand, first flatten and smooth out the leading edge. Make sure the leading edge goes into the laminator flat and parallel to the rollers. As soon as the rollers take the item, grasp the back corners and pull back and down on the item so the folds or wrinkles are pulled out and it is held flat against the feed tray going in. Don't lift up on the back of the item. Keep it flat against the feed tray.
2.2) If you see serious wrinkling on both sides of both film and paper, the laminating rollers probably need to be closed and locked. Check your roller opening/closing controls. (P.S. The laminating and pull rollers on an
Educator are always closed and locked.)
2.3) Wrinkling is hard to describe. What we mean by wrinkling is creases or folding over of the film or paper. What some people have described to us as wrinkling was what we would call waviness, or some other problem such as a repeating impression on the surface of the finished lamination. Sometimes the best way to identify the nature of a defect is to mail or overnight samples to us. Phone before sending in the samples. Label each sample clearly as to the type of film, laminator settings, and item being laminated. It's also a good idea to send un-laminated samples along for testing as well.
Film wrinkling with supply rolls moving from side to side
3.1) We see this symptom often enough that we decided to give it space by itself. This symptom indicates that the supply roll mandrels have been reversed. On an Educator or a Premier 4, look at the supply roll
tension knobs. The knob of the top mandrel should be on the right side of the machine (from the operator's view). That knob should have a decal which reads "TOP RIGHT." Likewise, the bottom mandrel should be on the right and should read "BOTTOM RIGHT." These two supply roll mandrels look identical, but they are not. When they get reversed, they don't apply supply roll tension, even when the supply roll tension knobs are tight. If the mandrels are in the correct position, but one is still slipping, the tooth which holds the supply roll core on the mandrel may be broken.
3.2) On HD or older Digital machines, the problem is similar. The supply roll mandrels only apply tension in one direction of unwind. If they are put in the roll of film backwards, it will not be possible to apply any supply roll tension and the film (supply roll) will move from side to side on the mandrel. The supply roll mandrels are interchangeable on these machines, but each mandrel has to be put in the film (supply roll) such that it can apply tension in the unwind direction. There are only two choices, so if one is wrong, the other must be right. If the placement is correct, but there is still no tension on a mandrel, its external gripping teeth or internal locking pin may be broken.
Bubbles or silvering between film and paper
4.1) A few large bubbles on the leading edge of the sheet being laminated is characteristic of what happens when the item is pushed into the nip faster than the speed of the laminator. As the paper buckles upward, the image side touches the top web of film in advance of the nip. Once captured in the adhesive, the bubbles cannot be removed. Bubbles can be captured in the same manner when the back of the item is lifted off the feed tray, or when the item is pushed too quickly as it is being fed.
4.2) Bubbles can be caused by lack of supply roll tension. Too little supply roll tension will cause bubbles before it will cause wrinkles in the film. See section 1.1 above for advice on setting supply roll tension.
4.3) As mentioned in sections 1.2, 1.3, and 1.4, bubbles and wrinkles can be seen if the film is not threaded correctly, if the temperature is too low, or if the laminating rollers are open.
4.3) Silvering is caused by the capture of tiny bubbles of air. It looks like a hazy or reflective area in the lamination. It may go unseen over light areas of an image, but will be more obvious over dark or black areas. Silvering is usually caused by too low an operating temperature. Silvering is most often seen when a machine is not given time to warm up or if the film temperature drops too low. When a large machine is warmed up without the motor on, one side of each laminating roller remains relatively cool. When lamination is begun, a pattern of repeated silvering can be seen each time the cool side of a roller is applied to the lamination. As will be mentioned again later, watch for any defect which repeats. This is typical of debris, damage, or low temperature on a section of the roller.
Repeating patterns or defects
5.1) This is a problem which has been known to baffle experienced laminator operators for a while. Fortunately, it's usually easy to fix. The circumference of the laminating roller on a Premier or Educator is about
four inches. The circumference of the roller on a HD-25 is almost five inches. The circumference of a HD or Digital laminating roller is a little over nine inches. Whenever you see those intervals on those machines, you will know there is something on the roller. That something is usually a piece of paper or a scrap of film. If the defect is adhesive, see the section below on cleaning the rollers.
Waviness or dimpling
6.1) This is usually caused by too much heat, forgetting to turn on the fans, or forgetting to close and lock
the pull rollers (this last item applies only to HD and Digital machines). The adhesive in the film needs to cool and solidify while it is pulled flat and tight between the laminating and pull rollers. If there is too much heat, or if the fans are off, or if the pull rollers are open, the adhesive will set up while the film is slack or curved, resulting in a clear but wavy laminated surface. Lines of distinct dimples which run down the center of the web at right angles to the laminating rollers are caused by excessive heat and/or forgetting to turn on the fans.
Smell of hot film
7.1) This problem is all too common in locations such as schools, where untrained operators and passers by have access to the laminator. There will always be someone who thinks that if 310 degrees is good for lamination, then 350 or 400 degrees would be better. You can sometimes spot these folks by the hot iron burn marks on their clothing. Never set your laminator hotter than 330 degrees Fahrenheit, and then only if you are using a standard 1.5-mil film. With 3-mil and thicker films, never exceed 280 degrees Fahrenheit.
Even when the temperature is at 310 degrees Fahrenheit with 1.5 mil film, some people will still find the hot film smell unpleasant or even nauseating. The good news is that the smell of hot polyethylene is not harmful to your
health. The better news is that you never need experience that smell again. There are now ultra low-melt films which will adhere beautifully at about 200 degrees Fahrenheit. Our favorite film is a very low-temp 3-mil which I usually run at 200 degrees for materials printed on a press and 240 degrees for inkjet printed materials.
Squealing while film is advancing
8.1) The squealing is caused by the taut film being pulled over the Teflon surface of the heat shoes. It is heard more often on new machines than old ones. Occasional shoe noise is normal on Ledco laminators (except ThermoGlide versions of the Digital machines). It is caused by too much supply roll tension, too little speed, or improperly coated laminating film. Squealing is usually eliminated by reducing supply roll tension and speeding up the machine. If squealing persists in spite of everything you try, the fault is probably with the film coating. Every once in a while, polyester suppliers send material to film makers which was coated for printing instead of being coated for lamination film. The print receptive coating is slightly sticky, while the proper coating for polyester in laminating film is a slip coat or a hard coat.
Cleaning the shoes and rubber rollers
9.1) Shoes and rubber rollers (especially the laminating rollers) should be cleaned each time film is changed. When cleaning is done regularly, it isn't a big chore. Adhesive of the shoes can be wiped off while the machine is hot using a clean, dry cloth. The adhesive will stick to the cloth much better than the Teflon on the shoe. Make sure to wear gloves or keep plenty of cloth between the shoe and your skin to avoid burns. If the
shoes have no adhesive on them, they can simply be dusted with a damp cloth. Never use any abrasive or solvent on the shoes. The abrasive can remove the Teflon, and solvents create a hazard with no benefits.
9.2) If there is no adhesive on the laminating rollers, they can likewise be wiped down with a damp cloth. You may use Windex or some other water-based solution which will not leave a residue. Except on the Premier 4 and Digital laminators, which have swing-away heart shoes, access to the laminating rollers is limited. On the Educator, the metal guard on the back of the top shoe can be easily removed for cleaning access. On HD machines, opening the laminating rollers offers access from the front. Never clean the machine when the power is on. Very serious injuries can result when people try to clean a laminator when the power is on. Clean one section of the rollers, then restore power and advance the rollers a little to clean the next section. Continue the process till the rollers are clean.
When there is adhesive on the rollers, warm the machine to operating temperature for 15 minutes with no film threaded. Open the rollers and leave them turning during warm up. Once the adhesive is heated and softened by the heat, disconnect power. While the adhesive is still hot, it can be removed with a hard rubber or plastic eraser or rubber cement pickup. These materials will cause the soft adhesive to roll up in little balls which can then be wiped off with a damp cloth. Observe the warning just above. Never clean the machine unless power is disconnected.
Heat settings. Understanding the variations.
All hot shoe laminators will overshoot the set temperature at initial warm-up and when pausing after a run. The heaters in the shoe stay on until the sensor in the shoe reads the set temperature. When the sensor reaches the desired temperature and shuts off the heaters, the heat cartridge is still red hot. That heat continues to travel to the surface of the shoe. It takes about 90 seconds for the heat to reach the surface of the heat shoe. This latent heat will push the temperature up 10 to 20 degrees over the set temperature before stabilizing. It will usually take about 10-15 minutes to stabilize on initial warm-up and unless the user is running the temperature at the maximum that the film can tolerate, it does not affect the lamination. The same is true when you stop after running continuously for a few minutes. It is always a good idea to run 6-12 inches of film before inserting a new piece into the laminator when it has been sitting for over 5 minutes as the film that has been sitting on the shoe tends to cook causing the adhesive layer to gel and be less effective.
If you are running PSA film and using a low heat setting (110-130 degrees F) as an assist to help the adhesive flow, you will notice an even wider fluctuation in temperature. This is because the small amount of heat required to raise the temperature of the shoe up 30 degrees over room temperature would only require the heater to run for about 20 to 30 seconds, so when the heaters are on for the 2 minutes, and the shoe reaches that low set temperature, the extra BTU's traveling through the shoe will push the temperature a good 25 degrees over that lower set point. The temperature will eventually stabilize but there will be wider variations. But this should not cause problems with the lamination.
Please contact us with any question or problem not covered here.
This is a reprint from Ledco.
Other products and companies referred to herein are trademarks or registered trademarks of their respective companies.
**Prices, images and specifications subject to change without notice.**
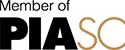

For your convenience, we accept these credit cards:
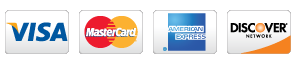